Cassava residue dehydration
Screw press successfully solved the problem of cassava residue dehydration
A large amount of cassava residue is discharged in the production of cassava starch, and 0.34-0.4 tons of absolute dry residue can be obtained per 1 ton of finished starch, which is an excellent raw material for the manufacture of full-price feed, food, chemical and other products.
At the same time, avoiding a large amount of potato residue into rivers and farmland is also an important measure to comprehensively control environmental pollution. If it is used for feed, industrial materials, storage, etc., it is necessary to dehydrate and dry the potato residue until the moisture content is greater than 15%.
However, the problem of dehydration of cassava residue has been troubling its comprehensive development and utilization, at present, the more ideal and effective method at home and abroad is the combination of mechanical and thermal energy method, that is, the mechanical method will remove part of the water from the potato residue, and then use heat drying (such as air drying, etc.).
Choosing normal mechanical dehydration method, such as, centrifugal hydroextractor, plate-and-frame filter press, vacuum suction filter, belt press, moisture content of wet slag semi-finished products is mostly between 65% and 75%.
However, our company after years of trial and error, and seriously summarize the lessons and experience of failure, has successfully developed a more suitable cassava residue, corn residue, all kinds of lees, cabbage, ulana, bamboo shoot residue, mushroom residue, stevia, beet, etc., and a variety of slag dehydration equipment (i.e., spiral dewatering machine, equipment model: ZTZY series), after production practice test, can basically solve all kinds of potato residue and other dehydration problems.
The advantages of this machine are small footprint, continuous production, low labor intensity and small investment. The use of special screen makes it easier to dehydrate the production process. The screen mesh hole is not easy to plug, and it’s easy to cleaning.
And the screw press dehydrate equipment has been updated. There are 1-50 cubic meters/hour capacity to choose, which suitable for various production requirements.
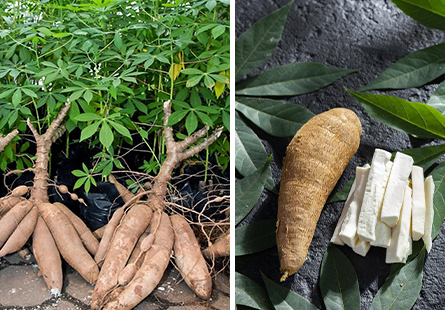
A large amount of cassava residue is discharged in the production of cassava starch, and 0.34-0.4 tons of absolute dry residue can be obtained per 1 ton of finished starch, which is an excellent raw material for the manufacture of full-price feed, food, chemical and other products.
At the same time, avoiding a large amount of potato residue into rivers and farmland is also an important measure to comprehensively control environmental pollution. If it is used for feed, industrial materials, storage, etc., it is necessary to dehydrate and dry the potato residue until the moisture content is greater than 15%.
However, the problem of dehydration of cassava residue has been troubling its comprehensive development and utilization, at present, the more ideal and effective method at home and abroad is the combination of mechanical and thermal energy method, that is, the mechanical method will remove part of the water from the potato residue, and then use heat drying (such as air drying, etc.).
Choosing normal mechanical dehydration method, such as, centrifugal hydroextractor, plate-and-frame filter press, vacuum suction filter, belt press, moisture content of wet slag semi-finished products is mostly between 65% and 75%.
However, our company after years of trial and error, and seriously summarize the lessons and experience of failure, has successfully developed a more suitable cassava residue, corn residue, all kinds of lees, cabbage, ulana, bamboo shoot residue, mushroom residue, stevia, beet, etc., and a variety of slag dehydration equipment (i.e., spiral dewatering machine, equipment model: ZTZY series), after production practice test, can basically solve all kinds of potato residue and other dehydration problems.
The advantages of this machine are small footprint, continuous production, low labor intensity and small investment. The use of special screen makes it easier to dehydrate the production process. The screen mesh hole is not easy to plug, and it’s easy to cleaning.
And the screw press dehydrate equipment has been updated. There are 1-50 cubic meters/hour capacity to choose, which suitable for various production requirements.
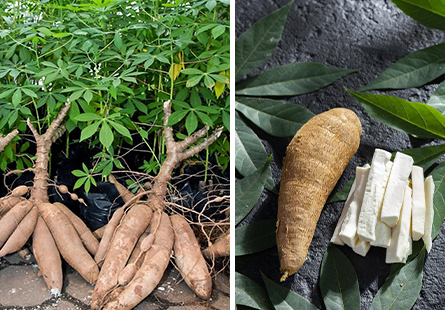
RECENT POSTS
Application
-
Paper pulp dehydrateHandling material: paper pulp; Capacity: 200t/d; There are many kinds of paper pulp, including bamboo pulp, wood pulp and so on. According to the different process there are acid method, chemical method and so on. We have different screw press dewatering machine which for different kinds of paper pulp. After dewatering Paper pulp is very dry. Till now, we have been exported to Australia and other countries.READ MORE >
-
Paint Residue DewateringReduces moisture from 70–80% to ~65%, depending on paint type, impurities, and equipment parameters (screw speed, screen size).READ MORE >
More Application